Producing an air flow meter for Mazda begins with a brief that looks deceptively simple: measure intake air mass quickly, report it accurately, survive 150 000 miles. Behind that sentence lies a chain of decisions that starts at raw-material selection and ends with a boxed sensor on a parts-store shelf.
First, every component is chosen for thermal stability. The sensing element—a platinum hot-film resistor—arrives on reels with certified resistance tolerance of ±0.1 %. Incoming inspection includes a salt-spray test to confirm corrosion resistance before the resistor is laser-welded to a glass-ceramic substrate. This step guarantees the air flow meter for Mazda will hold calibration in climates ranging from desert heat to sub-zero starts.
Next, the housing is injection-moulded from glass-filled nylon. The mould uses valve gates to prevent weld lines across the sensor bore, a detail that avoids turbulence-induced signal drift. Cycle time is 28 seconds; cavity sensors flag any short-shot instantly, diverting suspect parts to a rework loop.
Calibration is performed on a laminar-flow bench. Each unit is exposed to five air-mass points between idle and wide-open throttle. A 32-bit microcontroller stores the curve; a checksum protects against memory corruption. Once the air flow meter for Mazda passes ±1 % accuracy, the firmware is locked and the part receives a unique serial linked to the test log.
Packaging follows lean principles: trays nest six units deep, cutting freight volume by 40 %. A QR code on the tray links to installation videos, reducing customer-service calls. Finally, dual sourcing in Mexico and Vietnam keeps lead times under 21 days for orders up to 5 000 pieces, ensuring the repair market never waits long for stock.
By integrating precision sensing, robust calibration, and agile logistics, the plant delivers an air flow meter for Mazda that meets emissions rules today and hybrid strategies tomorrow—without drama, just dependable data.
Producing an air flow meter for Mazda
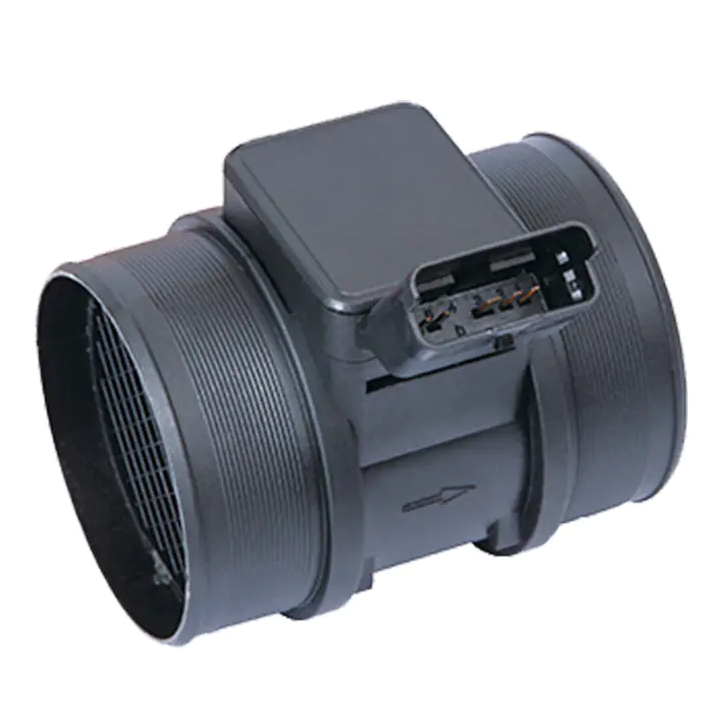