When designers want plastic to catch the light and shift colour like a pearl, they reach for Pearlescent Color Masterbatch. Across industries, the same concentrate turns ordinary resin into eye-catching surfaces, yet each sector tweaks the formulation to match its own workflow and end-use conditions.
In beverage packaging, converters spin 2 % of the masterbatch into translucent PET preforms. The platelets align during stretch-blow moulding, creating a champagne glow that travels the full bottle wall. Because the carrier resin matches PET’s intrinsic viscosity, streaks are avoided and cycle times remain unchanged. Retailers report higher shelf visibility under LED spotlights, while recyclers appreciate that the additive does not hinder post-consumer re-grind.
Cosmetics housings demand tighter colour control. A lipstick case manufacturer uses 3 % of the concentrate in ABS, adjusting mica coating thickness to hit a soft rose-gold hue. The masterbatch’s low-temperature carrier prevents thermal degradation during thin-wall injection, and the platelets survive ultrasonic welding that secures the cap.
Automotive interiors present another arena. Dashboard trim moulders blend 4 % of the masterbatch into heat-resistant PP, achieving a satin shimmer that hides fingerprints. Long-glass-fiber reinforcement is added downstream, yet the pearlescent layer maintains uniform orientation thanks to the platelets’ shear-thinning behaviour.
Even agricultural crates benefit. A 20-litre harvest basket uses 1.5 % of the concentrate in UV-stabilised HDPE. The gentle lustre signals quality at roadside stalls, while the additive does not block the UV package that protects produce during transport.
From bottle to dashboard, Pearlescent Color Masterbatch proves that a single additive family can adapt to vastly different applications when parameters are matched early.
Pearlescent Color Masterbatch in Real-World Applications
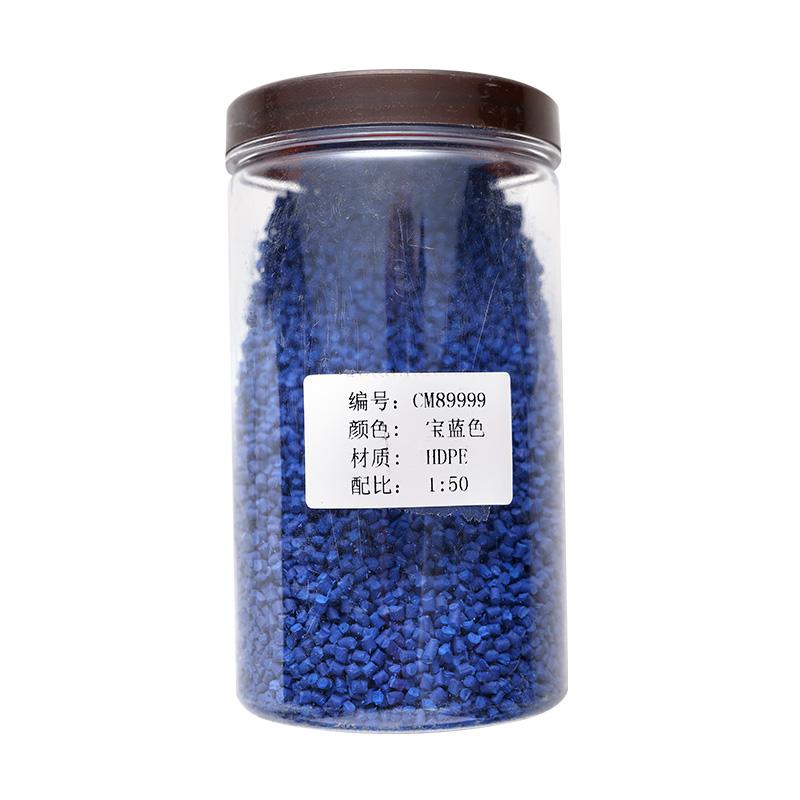