When a finished door meets the eye, the surface often appears to be solid timber. In reality, a veneer door skin is doing the visual heavy lifting while quietly delivering a list of practical benefits that solid wood cannot match. Understanding these advantages helps specifiers decide why this thin layer continues to win projects across residential, hospitality, and commercial sectors.
First, aesthetic consistency. Each veneer door skin is sliced from the same log section, then book-matched or slip-matched during lay-up. The result is grain continuity from top rail to bottom rail, eliminating the colour jumps common in stile-and-rail construction. Digital colour scanning keeps ΔE under 0.5 between batches, so a hotel corridor of fifty doors still reads as one continuous surface.
Second, dimensional stability. The skin is bonded to an engineered core—MDF, particleboard, or LVL—whose moisture movement is predictable. Laboratory cycling between 30 % and 80 % relative humidity shows thickness variation of less than 0.2 mm, preventing seasonal sticking or visible gaps. Architects appreciate that doors retain their reveal lines year-round without repeated planing.
Third, weight efficiency. A 3 mm veneer door skin adds roughly 2 kg per square metre compared with 12 mm solid timber, reducing hinge load and freight cost. Installers report easier handling on high-rise sites where every kilogram saved translates into safer lifting and lower crane charges.
Fourth, sustainability. Veneer is sliced at 0.6 mm thickness, yielding up to forty times more surface area than sawing the same log into boards. Off-cuts are returned to the core plant, and finishes are low-VOC, supporting green-building credits without premium pricing.
Fifth, finish flexibility. The same substrate can receive matte, satin, or high-gloss polyurethane topcoats, or even reactive UV-cured lacquer for scratch resistance. Abrasion tests with a 1 kg Taber wheel show negligible wear after 500 cycles, making the veneer door skin suitable for school corridors and hotel suites alike.
Sixth, acoustic and thermal add-ons. When paired with an insulating core, the skin contributes an extra 2–3 dB reduction in sound transmission and a modest R-value bump, meeting apartment acoustic codes without additional layers.
Seventh, repairability. Minor scratches can be spot-sanded and re-coated with matching finish; deeper dents are filled with tinted burn-in sticks that blend into the grain. This keeps maintenance budgets predictable over the product lifecycle.
From grain consistency to repair ease, the veneer door skin delivers a balanced set of advantages that justify its continued presence in modern building specifications.
Why Designers and Builders Keep Choosing This Finish
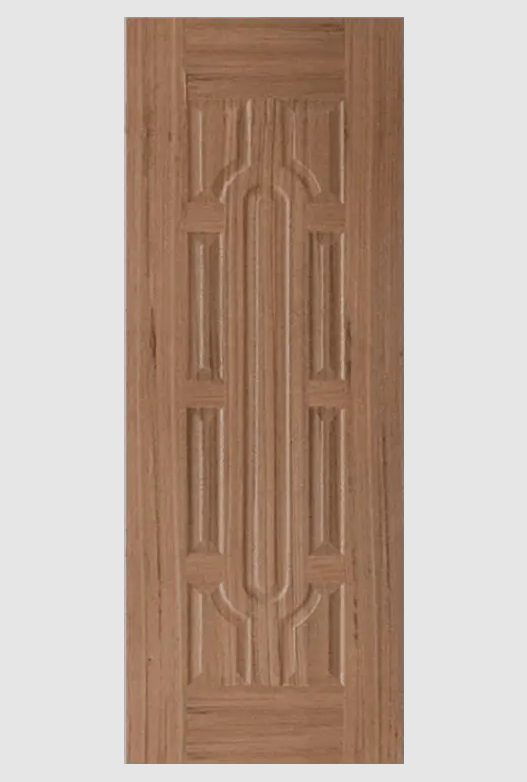