When a purchasing manager or small-business owner first searches for a Bucket Mould, the goal is rarely to find the flashiest design on the market. Instead, the search is driven by a quiet list of practical requirements that must be met if the finished bucket is to succeed in daily use. By walking through these needs in order of importance, buyers can short-list moulds that align with budget, timeline, and end-user expectations.
First comes volume and footprint. A farm-supply store that sells 15-litre feed buckets needs a mould with a cavity diameter near 300 mm and a height around 270 mm. Anything larger risks overfilling regulations, while anything smaller pushes customers toward competitors. Conversely, a janitorial supply company ordering 6-litre pails for window-cleaning concentrate prefers a cavity closer to 220 mm so the filled bucket remains light enough to carry up ladders. Users therefore begin by matching internal volume charts to real-world payloads rather than abstract litres.
Second is wall thickness and load rating. Construction crews often carry mixed cement in 20-litre buckets, so the Bucket Mould must produce a wall gauge of at least 2.0 mm to prevent bulging under weight. On the other hand, a food-processing plant filling buckets with berries needs thin walls around 1.3 mm to keep the tare weight low and reduce freight cost. Buyers typically request a sample shot and perform a simple stack-and-sit test before committing to production.
Third is handle ergonomics and strength. Users ask whether the handle socket is moulded in one piece or assembled later. One-piece sockets formed directly by the Bucket Mould avoid secondary labour but require more resin. Assembled handles allow colour contrast yet introduce a potential failure point. Buyers often bring a digital scale to the trial run, measuring the force needed to bend the handle 10 mm past horizontal; anything below 35 kgf is rejected for heavy-duty applications.
Fourth is sealing compatibility. Household storage buckets often need a gasket channel at the rim, while industrial chemical versions require a tamper-evident tear strip. Users therefore verify that the Bucket Mould includes the correct undercut geometry for either O-ring or lid plug, saving weeks of post-mould machining.
Finally, lead time and minimum order quantity enter the equation. A start-up launching a micro-brewery line may only need 5,000 pails to test the market, so the chosen Bucket Mould must be available as an off-the-shelf unit with existing cavities. Larger retailers, by contrast, can justify a custom design if it secures a long-term contract. By ranking these needs—volume, wall thickness, handle strength, sealing, and order flexibility—buyers can approach quotations with clear checklists and avoid costly revisions downstream.
Mapping Real-World Needs Before Placing an Order
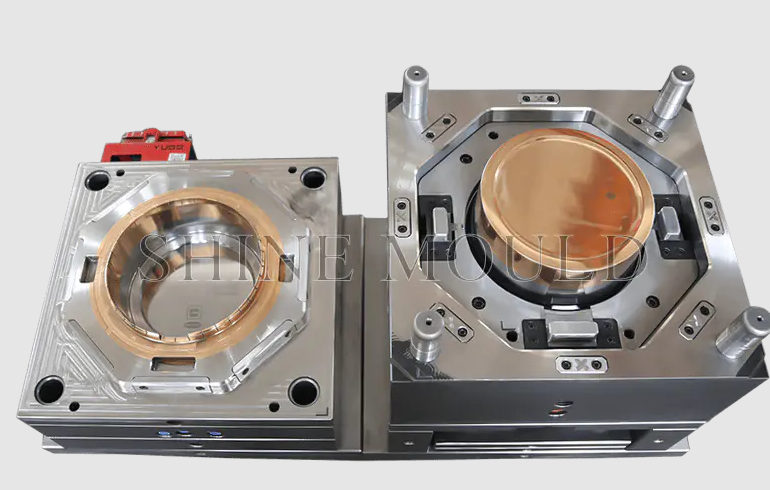